Friday, September 30, 2005
nano tube transistors
As reported in the May 20 issue of the journal of Applied Physics Letters, IBM researchers have improved carbon nanotube transistors. By experimenting with different device structures, the researchers were able to achieve the highest transconductance (measure of the current carrying capability) of any carbon nanotube transistor to date. High transconductance implies that transistors can run faster, leading to more powerful integrated circuits. Furthermore, the researchers discovered that the carbon nanotube transistors produced more than twice the transconductance per unit width of top-performing silicon transistor prototypes.
With today's announcement, IBM is taking carbon nanotubes, the strongest and most conductive fibers known, another step closer to becoming a viable option for replacing silicon transistors in future devices.
"Proving that carbon nanotubes outperform silicon transistors opens the door for more research related to the commercial viability of nanotubes," said Dr. Phaedon Avouris, manager of nanoscale science, IBM Research. "Carbon nanotubes are already the top candidate to replace silicon when current chip features just can't be made any smaller, a physical barrier expected to occur in about 10 to 15 years."
Today's achievement builds on a series of major research breakthroughs by IBM scientists using carbon nanotubes to make tiny electronic devices. Last April, IBM became the first to develop a groundbreaking technique (Science, Vol. 292, Issue 5517, April 27, 2001) to produce arrays of carbon nanotube transistors, bypassing the need to meticulously separate metallic and semiconducting nanotubes. Last August, IBM announced the world's first logic circuit within a single nanotube (Nano Letters, August 26 Web edition).
Creating the best-performing carbon nanotube transistors
The IBM scientists made single-wall carbon nanotube field-effect transistors (CNFETs) in a structure resembling a conventional metal-oxide-semiconductor field-effect transistor (MOSFET) structure, with gate electrodes above the conduction channel separated from the channel by a thin dielectric. They used these devices to study the performance improvements achieved by reducing the gate-to-channel separation. The top gate devices exhibited excellent electrical characteristics, including steep subthreshold slope (measure of how well a transistor turns on and off) and high transconductance at low voltages, a significant improvement to previously reported CNFETs which used the silicon wafer as a gate and a thick gate dielectric. The gate is an electrode that controls the flow of electricity through the device. Furthermore, the IBM scientists were able to fabricate both hole (p-type) and electron (n-type) transistors. The top-gate design allows independent gating of each transistor, making it possible to generate CMOS (complementary metal-oxide-semiconductor) circuits that have a simpler design and consume less power.
By creating CNFETS that are similar in structure to that of conventional silicon MOSFETs, the team was able to compare CNTs with silicon transistors. Usually transistor performance improves as the oxide thickness and channel length decrease. Although the nanotube devices were not optimized in this case, they still outperformed the prototype silicon transistor. The IBM Researchers concluded that as their gate length and gate oxide thickness decrease with further development, future CNFETs would likely outperform silicon transistors even more dramatically.
The report on this work "Vertical Scaling of Carbon Nanotube Field-Effect Transistors Using Top Gate Electrodes" by Shalom Wind, Joerg Appenzeller, Richard Martel, Vincent Derycke and Phaedon Avouris of IBM's T.J. Watson Research Center in Yorktown Heights, N.Y. is published in the May 20 issue of the journal of Applied Physics Letters.
Try this in notepad and be amazed
Friday, September 16, 2005
Hydrgen Tablets
But this was made false by the research of scientists of "Danish Institute of Technology of Denmark".This was possible for them after a long research of one-and-a-half year.
PROCESS:
Firstly the hydrogen is mixed with hydrogen.
Then it forms Ammonia(NH3).
This Ammonia is mixed with MAgnesium Chloride(MgCl).
Frmthis they made 9.1% pure hydrogen tablets.
USES:
Hydrogen can be used as an alternative fuel.
But because of the non-availabilty of it solid-state, it is dificult to use.
For example, to run a MARUTHI-800 for 500Km we need a tank with capacity 9 times that of the car.
But with this result we can soon see vehicles running with hydrogen .
Thursday, September 15, 2005
The nano I-POD
lick Wheel and the ability to hold 1,000 songs or 25,000 photos. iPod nano works seamlessly with the iTunes® Music Store, the world’s number one digital music service.
iPod nano is the perfect combination of innovative design, storage capacity and ease of use. Thinner than a standard #2 pencil and weighing only 1.5 ounces.
4GB iPod nano holds up to 1,000 songs and the 2GB iPod nano holds up to 500 songs
The seriously slimmed-down nano -- about a quarter of an inch (0.6 cm) thick, 3-1/2 inches (9 cm) long and 1-1/2 inches (4 cm) wide -- drew "oohs" and "ahhs" from the audience at the product release in San Francisco, outdoing the buzz generated by the Rokr phone, which some said failed to meet high expectations for design.
The nano players, either all black or all white, are nearly as small as the entry-level iPod Shuffle but sport click wheels and hold up to 1,000 songs.
The iPod nano uses flash memory chips to store songs and photos, rather than the hard-disk drives that the iPod mini and the larger iPods use.
Sunday, September 04, 2005
Image of Section of High Performance MEMS Post Actuato
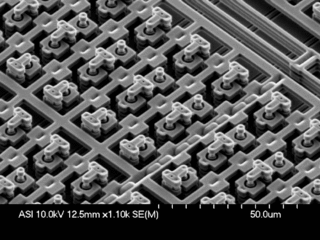
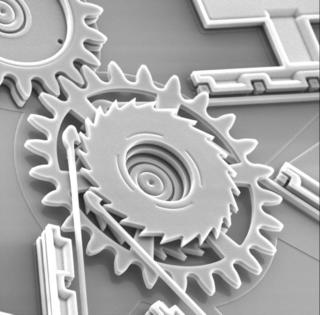
These are the High Performance MEMS Post Actuators.
For more imges please mail me to yaddanapudi1986@yahoo.com
MEMS Applications
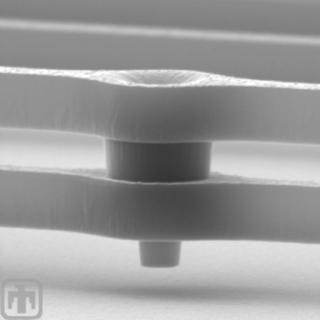
Imagine dust, floating in the air, gathering information on the weather, winds, humidity and pollution – all in a tiny cubic millimeter package. This is the “smart dust” scientists at UC Berkeley are developing in the laboratory today. Thousands or millions of these dust motes will sense the environment and communicate simultaneously using MEMS devices. Other applications under development range from such medical uses as hospital rooms that track patients and their medications and treatments, to the use of tiny surgical “scrapers” injected into arteries to clean out plaque, to military reconnaissance, to the detection of biological and chemical weapons.
Automotive: the first high volume application
After spending about 25 years in the lab, however, it was the automotive industry which first commercially embraced MEMS devices in the '90's as airbag accelerometers, recognizing the benefits of MEMS devices' small size, relative low cost and high degree of sensitivity.
Early airbags required the installation of several bulky accelerometers made of discrete components mounted in the front of the car, with separate electronics near the airbag (at a cost of over $50). Today, because of MEMS, the accelerometer and electronics are integrated on a single chip at a cost of under $10. The small size (about the dimensions of a sugar cube) provides a quicker response to rapid deceleration. And because of the very low cost, manufacturers are adding side impact airbags as well. The sensitivity of MEMS devices is also leading to improvements where size and weight of passengers will be calculated so the airbag response will be appropriate for each passenger.
There are many other automotive applications for MEMS either in use now or coming soon, including fuel pressure sensors, air flow sensors, tire pressure sensors with automatic built-in tire pumps, “smart” sensors for collision avoidance and skid detection, “smart” suspension for sport utility vehicles to reduce rollover risk, automatic seatbelt restraint and door locking, vehicle security, headlight leveling, and navigation.
MEMS come of age
Another wide deployment of MEMS is their use as micronozzles that direct the ink in inkjet printers. They are also used to create miniature robots (micro-robots) as well as micro-tweezers, and are used in video projection chips with a million moveable mirrors.
MEMS have been rigorously tested in harsh environments for defense and aerospace where they are used as navigational gyroscopes, sensors for border control and environmental monitoring, and munitions guidance. In medicine they are commonly used in disposable blood pressure transducers and weighing scales.
Out of these practical experiences have grown a raft of other applications which are quickly approaching everyday use. For example, engineers are utilizing the ability of MEMS devices to collectively assemble information and applying it to “smart roads.” Smart roads would be covered with millions of MEMS sensors. The sensors would act as a blanket of information, gathering and transmitting data about road conditions to people charged with maintaining them. Problems with roadways would be detected and repaired before they became serious. These smart roads could also send information to cars equipped with Global Positioning Devices, informing the on-board computer of road hazards, accidents, and traffic. Another safety application includes the detection of black ice on roadways and the development of windshields with automatic glare resistance.
Other arenas into which MEMS are moving include package shipping, where MEMS shock sensors would rest inside packages to monitor time and any type of damage that may occur while the package is in transit. One commercial application that is coming to market within months is a compact skin analysis unit for medical and consumer use, including department store cosmetics counters and pharmacies. This tool will contain small sensor-based units to analyze the physical and chemical properties of skin surfaces.
An additional and significant growth area for MEMS today is in telecommunications where the technology is being used for wireless applications as well as in optical networks.
MEMS Technology-manufacturing techniques
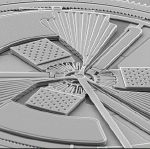
MEMS and ICs: two of a kind
MEMS microstructures are manufactured in batch methodologies similar to computer microchips. The photolithographic techniques that mass-produce millions of complex microchips can also be used simultaneously to develop and produce mechanical sensors and actuators integrated with electronic circuitry. Most MEMS devices are built on wafers of silicon, adopting micromachining technologies from integrated circuit (IC) manufacturing and batch fabrication techniques.
Like ICs, the structures are developed in thin films of materials. The processes are based on depositing thin films of metal or crystalline material on a substrate, applying patterned masks by photolithographic imaging, and then etching the films to the mask. In effect, a sacrificial layer is introduced – a material which keeps other layers separated as the structure is being built up but is dissolved in the very last step allowing selective parts of the structure free to move.
This use of established “batch” processing of MEMS devices, similar to volume IC manufacturing processes, eliminates many of the cost barriers that inhibit large scale production using other less proven technologies. Although MEMS fabrication may consist of a multi-step process, the simultaneous manufacture of large numbers of these devices on a single wafer greatly reduces the overall per unit cost.
Making the transition: from prototype to manufacture
Prototyping is integral to the process, however. An initial device is produced that can be characterized, measured, and optimized for performance and high volume manufacture. A key challenge can be the leap from prototype to high volume manufacture – a transition that sometimes requires considerable modifications. This requires the availability of broad-based design and process expertise (not just application experience), as well as appropriate software tools that can automatically provide process customization. CAD tools are crucial to a cost and time-effective process. Previously developed internally, there are now several commercially available CAD packages that guide engineering teams through component design, system design, and analysis.
It's important to note that MEMS manufacturing technology is not a uniform science but rather a combination of design techniques and knowledge of materials, process, and applications. Processes may vary considerably. For example, the techniques used for wireless may not work at all for the development and production of optical communications devices. Further, although MEMS and IC manufacturing is based on photolithographic etching, in many cases the processes and/or materials may not be compatible. It's interesting to note that gold, which is required in the manufacture of optical MEMS, will contaminate an IC batch.
There are three general approaches to the fabrication of MEMS: surface micromachining, bulk micromachining, and LIGA (lithography, plating, molding).
Surface micromachining is a process based on the building up of material layers selectively remaining or removed by continued processing. The bulk of the substrate remains untouched.
In bulk micromachining, large portions of the substrate are removed to form the desired structure. Structures with greater heights can be formed because thicker substrates can be used. The bulk micromachining process is a key fabrication method used for MEMS-based photonic switching in the high-growth optical and wireless markets.
LIGA processes combine IC lithography and electroplating and molding to obtain depth. Patterns are created in a substrate and then electroplated to create 3D molds. These molds can be used as the final product, or various materials can be injected into them. This process has two advantages. Materials other than silicon can be used (e.g. metal, plastic) and devices with very high aspect ratios can be built.
The fabrication process is usually a structured sequence of THREE BASIC PROCESSES:
1. Deposition
Deposition is a key building block in that it is the ability to deposit thin films of material (for subsequent local etching). MEMS deposition technology is classified in two groups:
Depositions resulting from chemical reactions: chemical vapor deposition, electrodeposition, epitaxy, and themal oxidation. These processes exploit the creation of solid materials directly from chemical reactions in gas and/or liquid compositions or with the substrate material. The solid material is usually not the only product formed by the reaction. Byproducts can include gases, liquids and even other solids.
Depositions resulting from physical reaction: physical vapor deposition, casting. The material deposited is physically moved on to the substrate (a chemical byproduct is not created).
2. Etching
In order to form a functional MEMS structure on a substrate it is necessary to etch the thin films previously deposited and/or the substrate itself. In general, there are two classes of etching processes:
- Wet etchng: the material is dissolved when immersed in a chemical solution
Dry etching: the material is sputtered or dissolved using reactive ions or a vapor phase etchant.
Lithography in the MEMS context is typically the transfer of a pattern to a photosensitive material by selective exposure to a radiation source such as light. When a photosensitive material is selectively exposed to radiation (e.g. by masking some of the radiation), the radiation pattern on the material is transferred to the material exposed (the properties of the exposed and unexposed regions differ).